Understanding Plastic Injection Molding Manufacturing
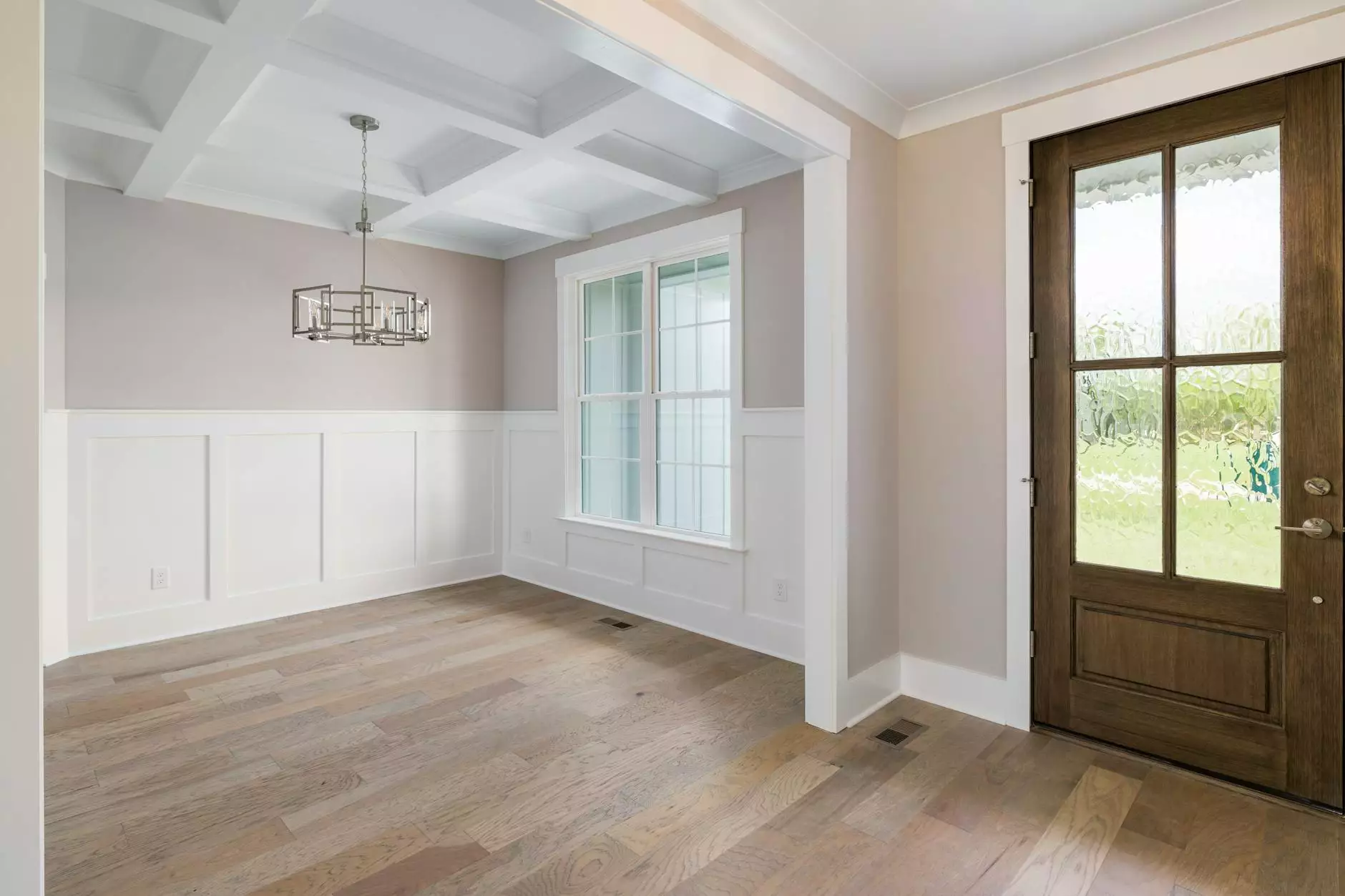
In the competitive landscape of modern manufacturing, plastic injection molding stands out as a crucial process that shapes the products we use every day. Whether you are in the automotive, electronics, or consumer goods industry, the impact of a reliable plastic injection molding manufacturer is undeniable. This article delves into the intricacies of plastic injection molding, outlining its benefits, processes, and the key factors to consider when selecting a manufacturing partner.
What is Plastic Injection Molding?
Plastic injection molding is a manufacturing process used to produce parts by injecting molten plastic into a mold. The process is highly efficient and versatile, allowing for the production of complex shapes and high volumes of products with consistent quality. Here’s how it works:
- Material Selection: The process begins with selecting the appropriate plastic resin, which can vary based on the product requirements.
- Heating and Injection: The selected resin is heated until it reaches a molten state before being injected into a mold under high pressure.
- Cooling: The molten plastic cools down in the mold, solidifying into the desired shape.
- Removal: After cooling, the newly formed parts are ejected from the mold.
Advantages of Plastic Injection Molding
The plastic injection molding manufacturing process offers numerous advantages, making it a preferred choice for many industries:
- High Efficiency: Once the mold is created, the process can produce a large number of identical parts in a short period.
- Cost-Effectiveness: Despite the initial costs of mold creation, the long-term savings from mass production can significantly reduce the per-unit cost.
- Design Flexibility: Injection molding allows for intricate designs that would be difficult or impossible to achieve with other manufacturing techniques.
- Material Variety: A wide range of plastics can be used, including thermoplastics and thermosetting plastics, offering manufacturers flexibility in their product lines.
- Consistent Quality: The automated nature of the process ensures a high degree of consistency and precision in the final products.
Applications of Plastic Injection Molding
The uses of plastic injection molding are virtually limitless. Some of the most common applications include:
1. Automotive Industry
In the automotive sector, plastic parts are crucial for reducing weight and improving fuel efficiency. Components such as dashboards, trims, and housings are often produced using injection molding.
2. Electronics Industry
Plastic injection molding plays a significant role in producing casings for electronic devices, connectors, and other components, ensuring durability and reliability.
3. Consumer Goods
From kitchen utensils to toys, many consumer products are manufactured using this efficient process, allowing designers to create aesthetically pleasing and functionally robust items.
4. Medical Devices
The medical field benefits greatly from plastic injection molding, as it allows for the production of sterile and precise components that meet stringent quality standards.
Choosing the Right Plastic Injection Molding Manufacturer
When selecting a plastic injection molding manufacturer, various factors come into play. Make sure to consider the following:
1. Experience and Expertise
Choose a manufacturer with a proven track record in the industry. Experienced manufacturers will have knowledge about different materials and techniques that can optimize production.
2. Technology and Equipment
Modern and advanced machinery is essential for high-quality production. Ensure that the manufacturer utilizes the latest technology to enhance performance and precision.
3. Quality Control Measures
A strong quality management system is vital. Manufacturers should have robust testing and inspection processes to ensure that products meet required specifications.
4. Customer Support and Service
Effective communication and support are key to a successful partnership. Choose a manufacturer that offers excellent customer service throughout the project lifecycle.
Environmental Considerations in Plastic Injection Molding
In today’s eco-conscious world, the environmental impact of manufacturing processes is more critical than ever. Many plastic injection molding manufacturers are now taking steps to minimize their ecological footprint:
- Recycling Initiatives: Many manufacturers are implementing recycling programs to reduce plastic waste.
- Use of Biodegradable Materials: The industry is gradually shifting towards more sustainable materials to create eco-friendly products.
- Energy Efficiency: Upgrading to energy-efficient machines can significantly reduce energy consumption during production.
Understanding the Mold Design Process
A successful plastic injection molding project relies heavily on the mold design. Here are the critical stages of the mold design process:
1. Concept Development
The first stage involves developing a concept based on the part specifications, including dimensions, tolerances, and material selection.
2. CAD Modeling
Computer-Aided Design (CAD) software is used to create detailed models of the part and the mold, enabling manufacturers to visualize the final product and identifying potential issues.
3. Mold Flow Analysis
This simulation assesses how the molten plastic will fill the mold, identifying areas that may lead to defects like warping or insufficient filling.
4. Prototyping and Testing
Creating prototypes allows manufacturers and clients to evaluate design and functionality before full-scale production begins.
Cost Factors in Plastic Injection Molding
The costs associated with plastic injection molding can vary based on several factors, including:
- Mold Complexity: More intricate molds require more time and resources to create, driving up costs.
- Material Costs: The choice of plastic resin significantly impacts overall production costs.
- Production Volume: Higher volumes can lead to lower per-unit costs, while low-volume runs may be less cost-effective.
- Lead Time: Urgent projects may incur higher costs due to expedited shipping or production.
Future Trends in Plastic Injection Molding
The industry is constantly evolving, and several trends are shaping the future of plastic injection molding:
1. Advanced Materials
As technology advances, manufacturers are exploring new materials that offer improved performance, durability, and sustainability.
2. Automation and Smart Manufacturing
The incorporation of automation and IoT (Internet of Things) technologies can enhance efficiency, reduce labor costs, and improve production accuracy.
3. Customization and Personalization
As consumer demand for bespoke products grows, manufacturers are adapting their processes to offer greater customization options.
Conclusion
In summary, working with the right plastic injection molding manufacturer can dramatically enhance your production capabilities, improve product quality, and ultimately drive your business's success. As the industry continues to innovate and adapt to the modern demands of sustainability and efficiency, partnering with a knowledgeable and reliable manufacturer is more important than ever.
For businesses looking to leverage the benefits of plastic injection molding, Deep Mould offers extensive experience and cutting-edge solutions that can help you achieve your goals. Explore what comprehensive expertise in plastic injection molding can do for your company today!