The Versatile Applications of Ultem in Industry
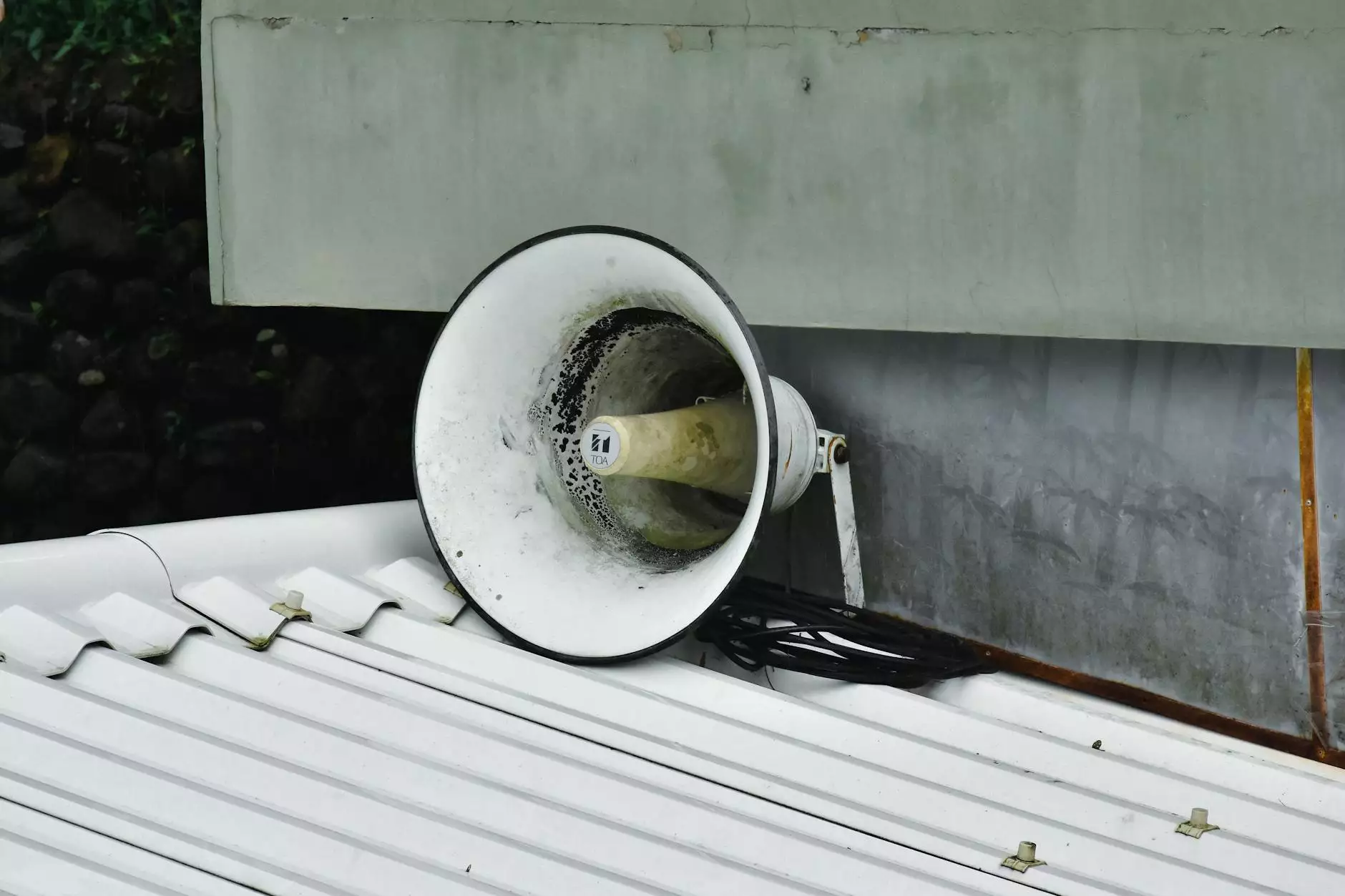
Ultem, scientifically recognized as polyether ether ketone (PEEK), stands out as one of the most remarkable thermoplastic materials in modern engineering and manufacturing contexts. Known for its exceptional mechanical, thermal, and chemical resistance, Ultem has become a material of choice in diverse industries, including aerospace, automotive, and medical device manufacturing. In this comprehensive article, we will explore the unique properties of Ultem, its applications in various domains, and its advantages over other materials, ensuring you understand why Ultem is a pioneer in high-performance engineering materials.
Understanding Ultem: Properties and Composition
Ultem is a polyaryletherketone (PAEK) with a unique molecular structure that endows it with properties that few materials can match. The following are key characteristics:
- High Thermal Stability: Ultem can withstand temperatures up to 200°C without deforming, making it ideal for high-heat applications.
- Excellent Chemical Resistance: This material is resistant to a wide range of chemicals, including hydrocarbons, acids, and bases, ensuring its longevity in various environments.
- Outstanding Mechanical Strength: Ultem exhibits high tensile strength and rigidity, allowing it to endure significant stress without failure.
- Low Density: As a lightweight thermoplastic, Ultem is favorable in industries where weight reduction is crucial, such as aerospace.
- Superior Flame Retardance: Ultem has inherent flame-retardant properties, making it a safe choice for electronic and automotive applications.
- Biocompatibility: Certain grades of Ultem are suitable for medical applications, where biocompatibility is essential.
Applications of Ultem in Different Industries
Aerospace Industry
The aerospace industry demands materials that can withstand extreme conditions. Ultem fulfills these requirements with ease. Components made from Ultem are utilized in various applications including:
- Structural Parts: Ultem's lightweight and robust characteristics make it favorable for manufacturing components such as brackets and supports.
- Electrical Insulation: Its excellent dielectric properties allow Ultem to be used as electrical insulation in high-performance aircraft electronic systems.
- Fire Retardant Panels: Ultem’s flame-retardant nature ensures safety and compliance with stringent aerospace regulations.
Automotive Applications
In the automotive sector, Ultem is leveraged for its combination of strength and lightweight properties, which are essential for fuel efficiency and performance. Common uses include:
- Under-the-Hood Components: Used for fuel systems, transmission parts, and engine covers, Ultem can handle the temperature and chemical exposures common in automotive environments.
- Interior Components: Its aesthetic appeal and durability make it suitable for trims and other visible parts of the vehicle.
- Electrical Connectors: Ultem’s superior insulation properties make it an ideal material for connectors that must operate reliably in challenging conditions.
Medical Device Manufacturing
Ultem is a go-to material in the medical field due to certain grades' biocompatibility and sterilizability, which are critical for medical applications. It finds use in:
- Surgical Instruments: The precision and strength of Ultem make it suitable for manufacturing surgical tools and device housings.
- ImplantableDevices: Certain formulations of Ultem can be used in implants due to its necessary compatibility with biological tissues.
- Diagnostic Equipment: Components like connectors and housings in diagnostic tools benefit from Ultem’s chemical resistance and stability.
Electronics and Electrical Applications
The electronics industry relies heavily on materials that are robust and possess excellent insulating properties. Ultem serves this industry through:
- Insulation Material: Ultem is frequently used as insulation for wires and cables due to its dielectric properties.
- PCB Components: It is applied in various printed circuit board (PCB) components, ensuring reliability in electronic devices.
- Connectors and Components: The resilience of Ultem allows for the design and manufacture of connectors that can withstand harsh conditions.
Advantages of Using Ultem Over Traditional Materials
Choosing Ultem for engineering and manufacturing applications brings a plethora of advantages when compared to traditional materials such as metals and other plastics:
- Weight Reduction: Ultem's low density contributes to overall weight savings, which is especially beneficial in aerospace and automotive applications.
- Reduced Maintenance Costs: Its exceptional durability and resistance to wear and chemical attack enhance the longevity of components, leading to lower maintenance costs.
- Versatility: Ultem can be processed through various methods, including injection molding, 3D printing, and machining, making it suitable for diverse applications.
- Environmental Resistance: Ultem’s ability to remain stable in harsh environments makes it a preferred choice over materials that degrade quickly.
- Performance in Extreme Conditions: Its high thermal and mechanical performance in extreme conditions gives it an edge over many traditional materials.
Innovation in 3D Printing with Ultem
The emergence of 3D printing has opened new avenues for utilizing Ultem in innovative ways. As a material for additive manufacturing, Ultem offers several benefits:
- Complex Geometries: Ultem can be printed into intricate designs that would be difficult or impossible with traditional manufacturing methods.
- Rapid Prototyping: Engineers can quickly produce prototypes using Ultem, streamlining product development cycles.
- Customization: 3D printing allows for the customization of parts per specific project requirements, making it easier to meet unique demands.
- Sustainability: Using 3D printing with Ultem can lead to less material waste during the production process compared to traditional machining.
Future Trends and Developments in Ultem Technology
The journey of Ultem in diverse industries is promising, with ongoing research and innovations that aim to expand its capabilities. Future trends in Ultem technology include:
- Advanced 3D Printing Techniques: Continuous improvements in 3D printing technology will enhance Ultem's printing capabilities, broadening its application scope.
- Hybrid Materials: Research into hybrid materials that combine Ultem with other substances could lead to even greater performance characteristics.
- Eco-Friendly Formulations: The demand for sustainable materials is influencing the development of eco-friendly versions of Ultem, enhancing its appeal in environmentally-conscious industries.
- Smart Materials: Integration of electronics and smart technologies into Ultem-based products may pave the way for next-generation applications.
Conclusion
In conclusion, Ultem stands as a testament to the advancements in materials science, showcasing its vital role across multiple industries through its unmatched performance and extensive applications. From aerospace to 3D printing, Ultem's unique characteristics ensure it remains at the forefront of engineering and manufacturing innovations. As industries continue to evolve, the adaptability and reliability of Ultem will undoubtedly facilitate the development of innovative solutions across myriad applications. Embracing Ultem is a step toward a more efficient, durable, and innovative future in manufacturing and design.
For all your requirements related to Arts Supplies, Product Design, and 3D Printing, consider exploring the offerings at arti90.com, where you can discover how Ultem and other high-performance materials can enhance your projects and products.